The 101 of good ship design – our experience in hull form and propulsion efficiency optimisation
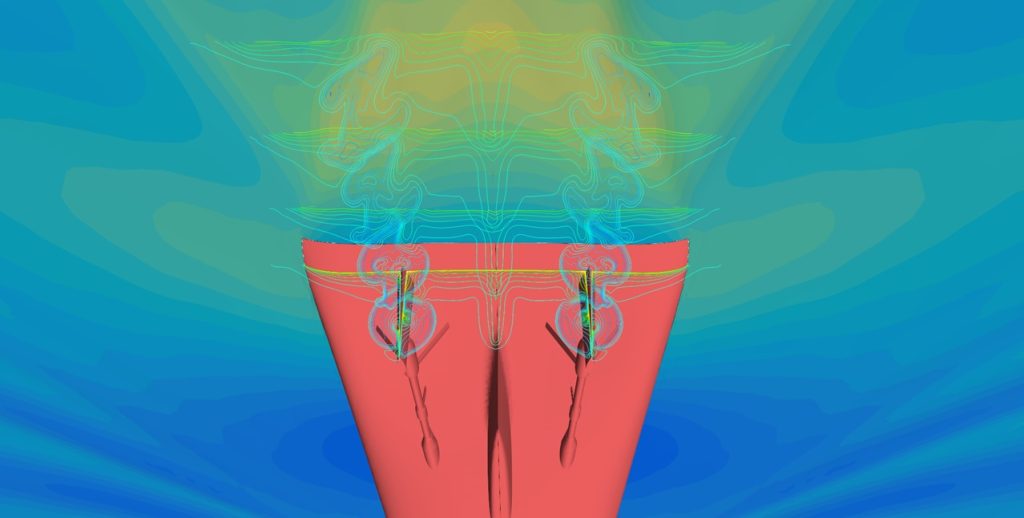
By Matias Niemeläinen, Head of Hydrodynamics, and Jyri-Pekka Arjava, Senior Naval Architect, fathers of Deltamarin’s flexible DeltaSeas tool for evaluating a ship’s power needs over its lifetime.
A strong foundation
From the energy and emissions perspective, ship propulsion is the largest onboard energy consumer, so the core of good design is ensuring an optimal layout and good hull/propulsion efficiency. Optimal hull form matching the dedicated operation of the vessel is one of the most important decisions during the ship design process, as the ship will be married to that one hull for its entire lifetime.
References ‘R’ us
It is necessary to have plentiful references, such as model test and sea trial results, from all types of vessels. Our comprehensive reference database enables us to give accurate predictions of ship propulsion power already at an early concept development stage.
All reputable professional ship designers and naval architects use computational fluid dynamics (CFD) to design best possible hull form and propulsion efficiency, as well as predict the vessels propulsion power accurately. However, to get the most out of CFD we also need experienced hydrodynamics specialists and experienced CFD users/developers.
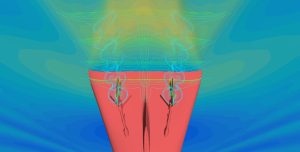
The validation process has taken a long time and included a lot of software development and especially gaining expertise in-house, as there was no programming for correction factors. (Depending on ship type, speed etc., the correction factors used on top of CFD results to produce speed-power predictions are different). The know-how gained from working on the reference projects is essential – you need to know all the fine detail to generate an accurate prediction of propulsion power.
Benefits of ‘cross-fertilisation’
Our practical experience in designing all main ship types has been invaluable and is something only very few companies have. For example, the superior form of our bulk carriers’ stern shape was inspired by passenger vessel designs, which at the time were very different from traditional bulker designs. In addition, we were the first to apply a vertical stem to our B.Delta bulk carrier designs to reduce resistance, and they have since become more popular on almost all other ship types. In contrast, some shipyards typically design and build only a limited range of ship types, which is not conducive to this kind ‘cross-fertilisation’ of learning between ship types.
Good design precedes technologies
When we introduced our B.Delta bulk carriers to the market in around 2010, they were much superior in efficiency and decades better in terms of fuel consumption than existing shipyard designs. But how much better can a ship hull actually become?
Although today we can’t expect pure hull form development to generate the same kind of huge improvements at design conditions, we have been able to boost total efficiency over 10% due to innovative designs and better simulation tools and practices over the past 10 years. And with highly developed CFD we can model a huge amount of other performance-influencing details than just hull resistance.
Carbon intensity is the holy grail
We see this continuous improvement in every ship type we design. However, ship projects often have limitations regarding main dimensions or cargo demands etc., and as designers we never have a completely free hand to create the best hull. But it is good to challenge these limits especially now when the goal for both designer and owner is to attain the lowest possible vessel carbon intensity. Since we do the whole design ourselves, we can study different alternatives in-house.
The desire for a low carbon footprint has also triggered a lot of interest in various energy saving devices (ESDs), which we typically use in our designs to further enhance total efficiency. We have experience of all major ESDs such as Air Lubrication, pre-swirl stators, rudder bulbs and so on. However, not all ESDS now available will be profitable if the baseline hull is very low consuming. From experience we know which ESD technologies are beneficial to specific hull and ship types.
Real-world conditions
It has always been important for us to understand how the ship will operate and how efficient our design is in real-world conditions. We are not a typical ship design company in that we often design the vessel from the conceptual design stage right the way through to basic or detailed design. This behoves us to take responsibility for the ships’ performance first in sea trials, but very soon after that they will have to report on their carbon intensity. Conducting realistic simulation of the design in action is therefore vital, and at Deltamarin we are already well equipped to do this.
In DeltaSeas, metocean statistics and wave and wind simulations are used for defining propulsion power for the entire operation life. All waves. All winds. All seasons.
Several years ago, we introduced our proprietary DeltaSeas method that allows us to evaluate added resistance due to weather conditions from a large number of cases. With clever use of CFD we can study propulsion power in different sea conditions and connect that information to weather data in dedicated geological areas where the vessel is intended to sail. The end result is a lifetime propulsion power profile for the ship.
Holistic modelling is the future
The future of hydrodynamics development is all about focusing on the big picture using big data. It’s where design and technology optimization meet. Up until now, designers have had only minimal data from live ship operations to serve as a continuous feedback loop on designs. Data has been typically limited to sea trials. However, since starting to receive operational data from customers we can now connect newbuilding designs to wind and wave data, enabling us to identify exactly where the development focus should be.
Operational data also shows that even today, design conditions (drafts and speeds) defined at the conceptual stage do not necessarily match the actual operation of the vessel. Using sophisticated holistic modelling makes it possible to still take big steps in optimizing the powering performance and the entire ship concept. This provides new opportunities to improve performance throughout the vessel life cycle, right from the design stage.
Our current EU project CHEK focuses on further improving our DeltaSeas tool by generating a more accurate interaction model of the ship hull and propulsion-related systems, based on a realistic operational profile. We’ll be talking about CHEK in our next blog.
For more information, please contact:
Matias Niemeläinen
Naval Architect, Hydrodynamics
matias.niemelainen@deltamarin.com
Jyri-Pekka Arjava
Naval Architect, Hydrodynamics
jyri-pekka.arjava@deltamarin.com
Want to read more? See also our other published blogs.