Evaluating project performance in a new business environment
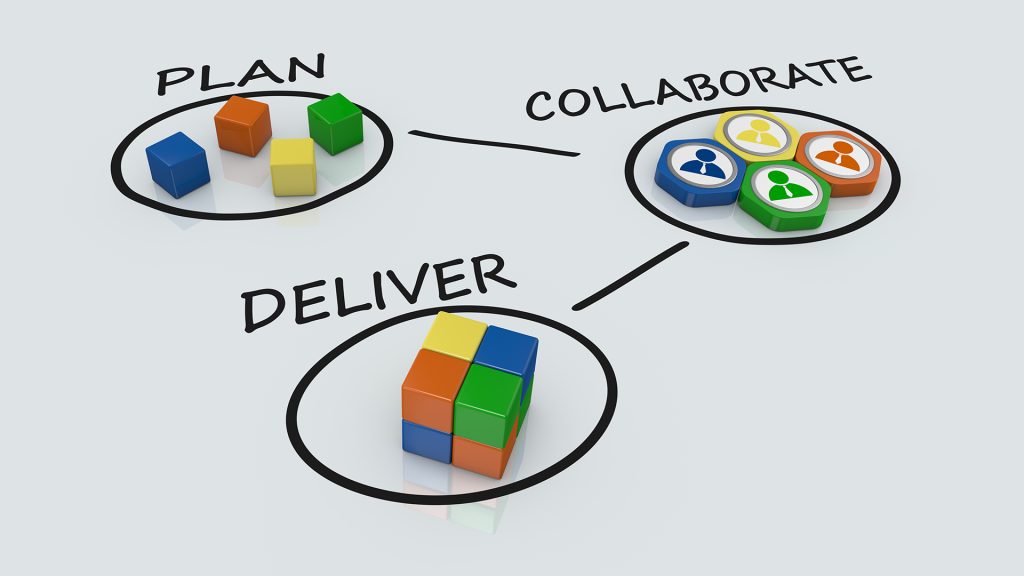
I am sharing my thoughts and experiences on the challenges and possibilities of measuring project performance in shipbuilding in a new business environment.
The modern shipbuilding projects are very complex and there are many stakeholders, for example the shipyard and ship owner, design house, classification society, interior architects, suppliers, etc. When entering a new business area, such as building a more challenging ship type like passenger ships, the amount of new information is extensive, not only technically but also from the execution viewpoint. The change from merchant ships and a serial type of building towards complex one-off or prototype building is very challenging. Also, from the owner perspective, it is important to recognise how the different phases affect the whole project execution. In this article, I present a few good practices which, in our experience, are useful in the new complex project environment and in evaluating project performance.
Typically, the ship newbuilding development phases can be divided into two main sections:
- Pre-shipbuilding contract activities
- Post-shipbuilding contract activities
To ensure successful ship delivery, the most critical aspect is for the pre-contract project planning to be executed in a precise and logical manner. Delays or postponements in decision-making will lead to delays in the construction phase and eventually to an unforeseen increase in costs. The bases for successful project execution and construction phases are set even before the shipbuilding contract is signed. After the contract, there are very limited possibilities to make changes to the design and to project execution.
During the pre-contract phase, it is already essential to prepare plans regarding construction phase requirements in parallel with technical development. These activities include at least determining the following:
- Project execution model and organisations
- Engineering strategy
- Procurement strategy
- Building strategy
These items form a basis for creating performance indicators for each specific project.
Basis for project performance, schedule cost and quality
In principle, measuring performance may be easy to understand and utilise and I will not go into either basics or details in this text. There are many recognised and typically used indicators that normally evaluate and measure performance.
However, measuring performance is more challenging in the new market environment, for instance when starting to build new ship types. My focus in this text is project performance measurement, but it is also necessary to emphasise the key design performance indicators. Even though these (project and design indicators) can be considered separate topics, they are heavily linked and affect each other. The ship’s key design performance indicators are followed during the entire life cycle of the ship, whereas project performance is typically limited to the delivery of the project.
The credibility of measuring performance also relies on available and reliable statistical information, knowhow and experience. In the traditional business environment, there are usually some applicable statistics available, but in the new business environment or market it is more challenging to determine the basis for measuring performance. It is also essential to understand, that the design process can include a different variation for future-proofing purposes, which needs to be carefully considered when evaluating and selecting the performance indicators.
Basis for decision-making, criteria and especially the time required for decision-making
The first step is determining the project-phase objectives and goals and ensuring that all stakeholders share the same vision. We need to identify the critical success factors and understand their relations. It is essential that the objectives and goals are concrete, measurable and easy to comprehend and follow. These can be also described as project deliverables.
The deliverables set a reliable base for project planning:
- Scope
- Time
- Cost
- Quality
By setting the deliverables, we can define the limits for project, identify the known factors and also understand and quantify the still uncertain items. This is a valuable aspect when considering managing and mitigating risks. Once we have the targets set, it is easier to define the factors to follow and measure. Furthermore, agreeing the phase goals reduces the risks of confusion, misunderstandings, uncertainties and unpredictable events.
The performance indicators should give a reliable overview of project status, design, scope, time, budget and quality, on any given day. Furthermore, the performance indicators should give a solid basis for evaluating and preparing the decisions for further actions but, in the new business environment, perceiving the impacts of each decision may be difficult, as it is very challenging to understand the dependencies of different actions and tasks.
How to measure that we are successfully executing the project
When evaluating progress against planned schedule and budget, we have an indication of whether the project is going to meet the objectives and expectations. With properly prepared plans, we have the possibility to identify the causes of scope creep, possible delays or cost overruns and thus reduce the number of uncertainties and unpredictable events. There are multiple reasons that may cause variances, for example wrong initial estimates, assumptions, changes and modifications, resource allocations, etc. These causes may be identified, then the necessary decisions and actions need to be made to get the project back on track. However, it may be challenging to identify how decisions (or non-decisions) affect scope, schedule and thus also costs.
Especially in the new market environment, it is challenging to define the indicators, as the statistics from earlier projects may be considered non-existent or unsuitable for the new project. What we have noticed, however, is that there are many suitable bases for indicators that can be utilised, even from less experienced builders. The key is to identify the special features of the new ship type and find enough correct references from earlier projects, for example concerning effectiveness, productivity and lead times. We can then develop these available statistics with valid coefficients to be more suitable for the new projects.
In fact, in our experience we can say that the main challenges are actually not in the technical details, but in the processes – how the project is managed and what items are key in different phases. Although shipbuilding includes similar processes in general, currently used processes may not be applicable as such in the new ship type. We must therefore identify differences in these processes and define the performance indicators accordingly. To ensure performance and project deliveries, it is crucial to understand when each decision should be made during the execution phases and what the expected impacts of delaying the decision are. It should be also clear to everybody which stakeholder has the responsibility for making a decision at a given time.
Importance of project planning decisions before a shipbuilding contract
The only way to ensure project performance (scope, time, cost, quality) throughout each and all execution phases is to concentrate on project planning before the shipbuilding contract is signed. There are not many possibilities to make changes afterwards without affecting the schedule and/or cost measures.
The focus is often on specifying the project’s technical perimeters in detail, which sets the basis for cost and quality requirements. However, there is typically a limited amount of technical information available at the pre-contract phase and there might even be many design variations. The number of details will increase during the following design phases. The performance can be measured reliably only by having selected and prepared the correct indicators for each project phase, including following the key design performance indicators. It must be recognised that scope and delivery is not only limited to technical productivity, but also to the overall efficiency of the processes.
Extensive project planning must be executed during the pre-contract phase. It is essential to be able to consider the details, which are still unknown when preparing the performance, even in the early phases of the project. With this, we are ensuring the scope, schedule and costs and limiting risks.
Summary and conclusion
To ensure project progress and fluent execution, the making of timely decisions is critical. It is essential for performance that extensive project planning be prepared during the pre-contract phase. To ensure the performance, the project must be broken down into concrete deliverables.
In addition, it is important to prepare plans for project execution to be able to select and utilise reliable performance indicators. This way, it is possible to ensure successful delivery in accordance with the promised schedule, to keep the budget and to fulfil the quality requirements.
We will later present a few case examples of how we have developed and ensured the project schedules in the new business environment together with our partners.
Want to read more? See also our other published blogs.
For more information, please contact
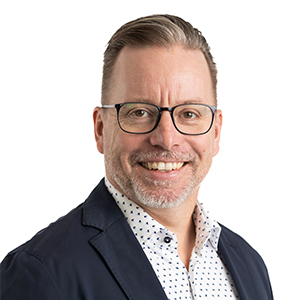