The low carbon story – part three
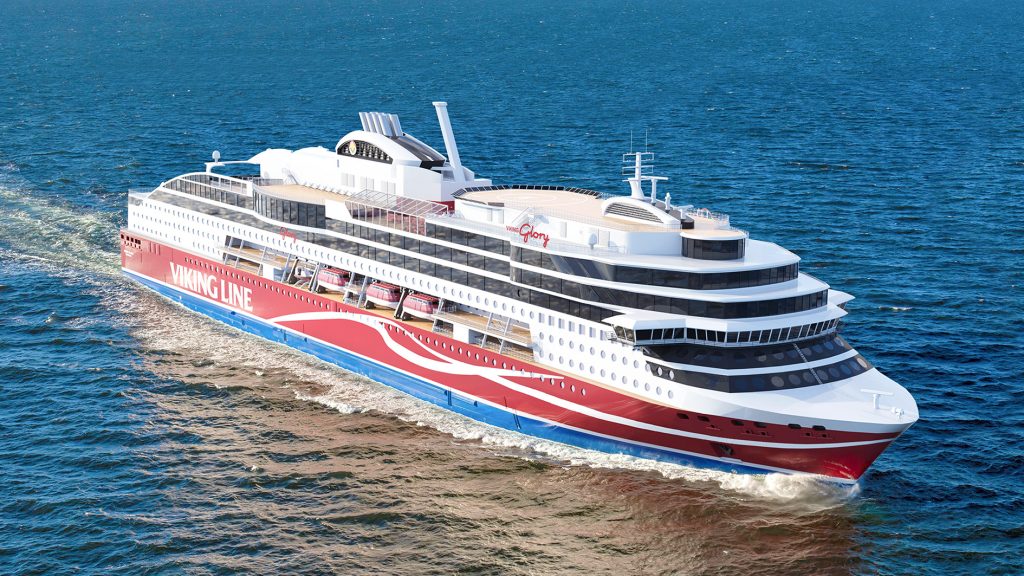
Energy efficiency in a newbuild vessel
Even though it is always interesting to read about new technology and new kinds of ships, such as the zero-emission cargo ship I told you about in the second part in our series on low carbon story, it’s also good to be reminded of the basis of sustainable ship design. I therefore now present a case story about the process of modelling and evaluating energy efficiency in a newbuild project. It’s the third, and at least for the time being, the final part in my small series on low-carbon ship design.
The low carbon story will also be a small part of the new upcoming Elsevier book Sustainable Energy Systems on Ships, which will provide holistic views on modern energy-efficient technologies and design methods in shipping.
Viking Glory from an energy engineer’s point of view
Deltamarin designed the Ro-PAX ferry, Viking Glory, that is currently being built at Xiamen shipyard in China. Viking Glory will have a capacity of 2,800 passengers and cargo lanes of 1,500 metres in addition to running on liquefied natural gas (LNG). This new environmentally efficient ship is due to enter service on the Stockholm-Åland-Turku route in early 2022. Deltamarin developed the vessel concept together with Viking Line, and assisted during the tender and contract phases.
The design project had a tight focus on energy- and environmental efficiency from the start. The new ship will be operating on the same route as the current flagship, Viking Grace, that was delivered in 2013 and she is supposed to be even more efficient. This meant that ship energy modelling was involved from the beginning of the project to study the impact of various design improvements and to benchmark key performance indicator (KPI) development in general.
Special attention was paid to hull form development and the propulsion concept, overall energy efficiency, weight control and improvement of the general arrangement. In addition to this, power production efficiency was expected to be high with the new Wärtsilä 31- dual-fuel engines. The ship power plant efficiency was further improved by including in the ship an extensive and unique waste heat recovery system consisting of Organic Rankine Cycles (ORC) at two temperature levels and steam turbines. The waste heat recovery plant converts part of the waste heat into electricity for the ship processes. Especially in the RoPAX type of ship, there is often plenty of waste heat available due to relatively high operating speeds, low heating load for consumers and, in this specific case, fast turnaround in port. In general, this equation often results in fast payback time for this type of energy-saving devices.
Ultimately after the concept design stage, it could be concluded that, even with one additional lane (resulting in larger breadth for ship), the vessel consumes less fuel than Viking Grace. The overall KPI improvement considering fuel consumption per lane meter in the route was over 15% based on the energy models.
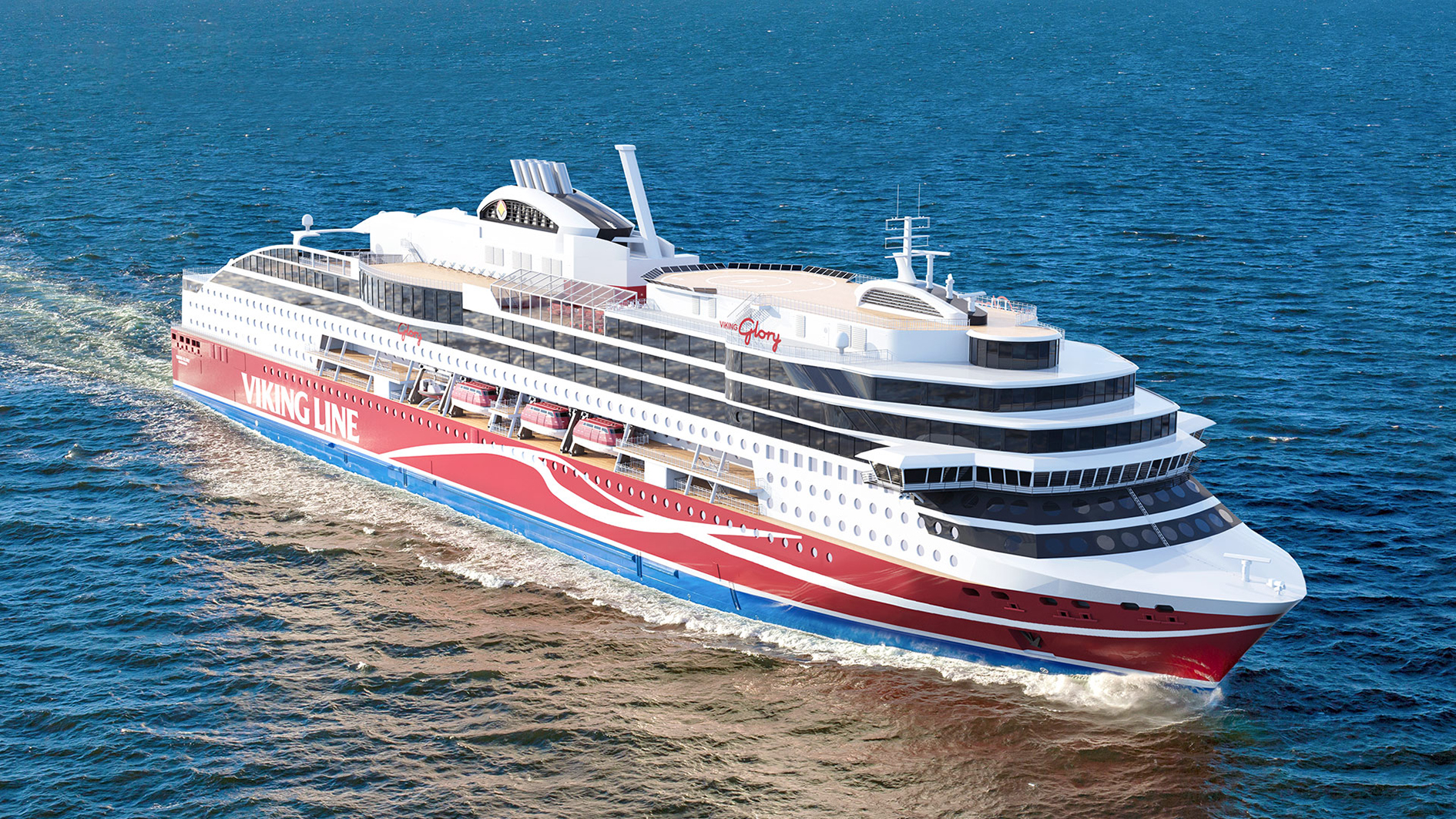
Energy modelling from conceptual stage to supporting the basic design phase
Energy modelling was done from the very beginning of the project by utilising operating speed measurement data from the Viking Grace energy management system. Design values for the ship’s propulsion power production, electricity and heat consumption were included in the energy model, in addition to the ship machinery and fuel data. The engine maker provided information on fuel consumption, exhaust gas temperatures and flows, as well as cooling water production. Several rounds of calculation were performed on alternative concepts for ship propulsion, electricity distribution and waste heat recovery. The results were documented in the ship’s KPI follow-up document that was included in the energy efficiency report during ship concept generation, and the process provided decision-making support for technology selection.
Special attention was paid to energy modelling in waste heat recovery system development, since the maker of the waste heat recovery equipment, Swedish Climeon, had previously retrofitted one small Organic Rankine Cycle unit on Viking Grace. The units for Viking Glory will be new-generation, but the data from the existing unit provided an important verification platform for the equipment maker. Deltamarin received a mathematical calculation model for the ORC unit electricity production within the feasible waste heat and cooling water flow- and temperature range, which was combined with the energy simulation model. This enabled very realistic simulation of the produced electricity, considering the energy system and all other ship design choices and technologies simultaneously. The model was utilised to give decision-making support to the designers in questions related to waste heat recovery and fresh-water cooling system dimensioning and architecture.
The energy model was also utilised after the concept design phase to support basic and detail design phase calculations for various smaller tasks. The most relevant ones included, for example, support in the dimensioning of and practical arrangements for the LNG cold recovery and LNG evaporation systems. The ship will utilise the cold evaporation energy of the fuel to provide direct cooling for certain selected consumers. For the energy model, this required adding only minor updates regarding the LNG cold recovery and details considering ship cooling system capacities and flows in the model.
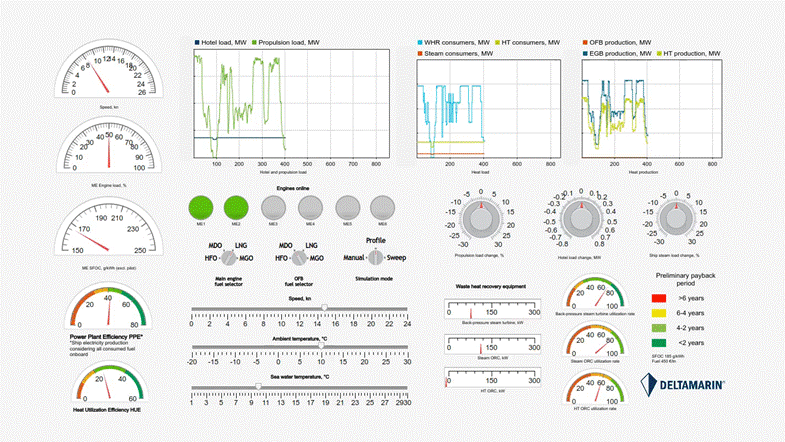
Practical lessons from the approach
Modern ships have complex technology onboard with numerous interconnections to other ship processes like the waste heat recovery system in the example case. Energy modelling is a necessary tool in the process of recognising the most relevant solutions and being able to dimension equipment for the purpose. In future when rules enter into force regarding carbon intensity indicator calculation for ships, energy modelling will be the method for evaluating the new ship carbon index. Therefore, even if energy modelling and energy efficiency as a design discipline are a fairly new part of the regular ship design process, it is definitely here to stay as part of each new project.
I hope that my low carbon story about shipping decarbonisation will help to concretise both the technical work and design considerations required. In addition to this, the idea of these blogs was to emphasise the increasing need to cooperate more intensively as a designer with ship owners, operators, equipment makers, shipyards, legislators, classification societies, researchers and other essential parties in the process. It’s indeed great to be an engineer today and help to make the world a bit less polluted!
Want to read more? See also our other published blogs. Here are also links to the first and second parts of the low carbon story.
For more information, please contact
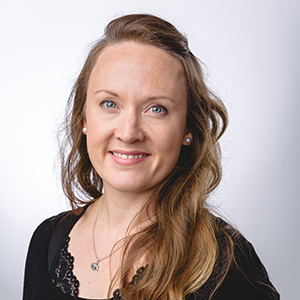