Using 3D models is a game-changer for ship design, but what does it mean in practice?
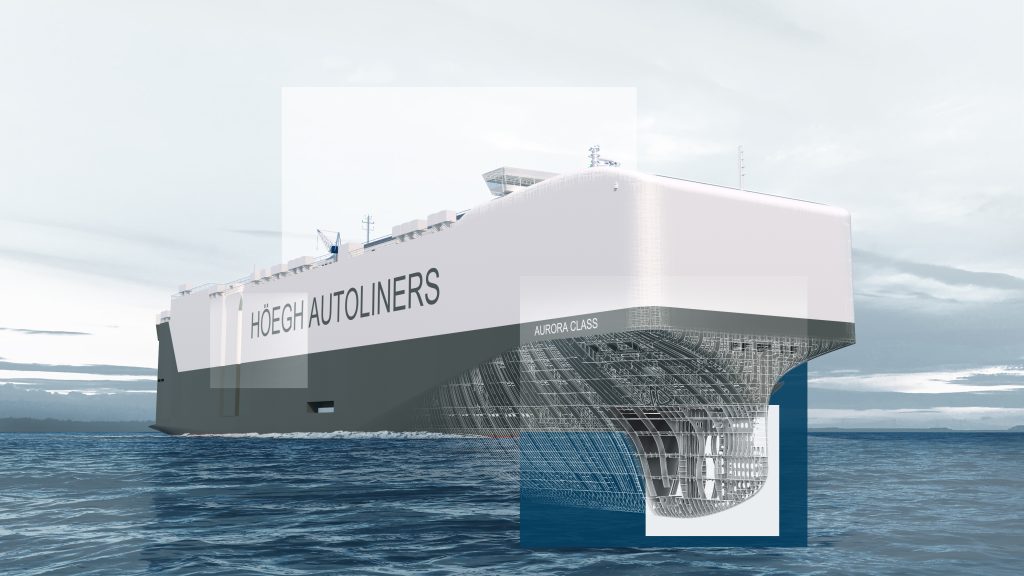
The use of 3D ‘digital twins’ for class approval represents a milestone in our ongoing focus on applying digitalisation to increase productivity and shorten the calendar time for ship design, writes Joonas Määttänen, project engineer at Deltamarin’s concept design department.
Designing ships in a 3D digital environment is not in itself new. We already use advanced CAD software in our everyday work, and these applications get better with every new release. However, what we can’t yet do is to use the 3D models themselves for the classification approval process, where the relevant class society could review and comment on the design directly from the models.
Goodbye to the analogue method
The traditional approval process – and this applies across the board – still requires us to supply the relevant class society with a vast amount of 2D structural drawings for every ship project. These we have to extract from the 3D models we have created, which is hugely time consuming. The effort that goes into them only increases as they get more detailed. For example, we recently built a detailed 3D model for the initial basic structural design of a regular-size Ro-pax vessel. From this we had to extract up to 50 separate sets of drawings each consisting of up to 1,000 individual drawing sheets. That is quite a mountain of material.
On average, around one-third of the basic design process on each project is spent on creating, modifying and updating such drawings, even though we do pretty much all of the actual design work in 3D. However, this is about to radically change as class societies increasingly work directly from 3D models. Our ultimate goal is to create an easily maintainable 3D models covering the basic design of entire ships – essentially a digital twin for class approval.
Reducing project lead times, enhancing production efficiency
Cutting out the laborious phase of generating and constantly updating 2D drawings we estimate will save up to 30% of the man hours required for the basic design process while also enabling faster ship deliveries. The class approval process, which is critical in terms of the ship’s overall delivery schedule, could in turn be completed around three months faster as the class surveyors can respond much quicker to the designer’s needs. Overall project lead time can be significantly reduced and productivity increased as the 3D model can be shared directly by all project stakeholders, including the shipowner, shipyard and equipment suppliers.
One crucial benefit of using a 3D model versus 2D drawings is that there is no room for “interpretation” as everything is visible in the model. The model’s automatic tools can highlight changes and show previous revisions, making it easy to track changes and revert to an earlier version if necessary. In addition, production can continue directly from the finally approved model, making handover to the shipyard easy, efficient and free of mistakes.
Life-cycle benefits
The interactive model also has life-cycle benefits that drawings cannot provide. The problem with drawings is that they quickly become obsolete and unusable as the ship’s structure changes, and not all drawings may even be available or accessible at a later date (some serve only one purpose after which they are no longer needed). In contrast, the digital twin would always be up to date as new changes can be done directly in the model. It would hold all important data in one place that everyone can access. Hence the benefits of the model accumulate over the ship’s entire life cycle – from initial classification to later modifications or conversions/retrofits with, for example, new propulsion systems including wind power. The production model can simply be handed over to the project-responsible designer and/or shipyard.
As Ole Christian Astrup, Senior Principal Specialist at DNV, confirms, using 3D models “opens up for new possibilities in asset data management, which I strongly believe will drive the safety and reliability of ship design and operation. A good example would be a more efficient process for verifying rule compliance. The OCX format will help designers to control and optimise their designs, while enabling class societies to confirm rules compliance directly from the 3D model”.
Deltamarin in the OCX vanguard
We are taking a leading role in this design evolution, having recently completed a section of the steel design work for an ammonia-ready Aurora Class vessel for Höegh Autoliners both in 2D and 3D, with the 3D model conforming to the new Open Class 3D Exchange Format (OCX) standard. The model was approved by DNV, which to our knowledge is a world first (see the press release here).
The OCX is standardized file format and key enabler to replace 2D documentation requirements. The standard is owned and managed by the OCX Consortium, which was established in 2021 and unites all the major class societies and CAD software vendors, as well as shipyards and design houses. The core objective is to break down barriers between different design platforms to enable the exchange of geometry and metadata between them. This will ensure that trace information is exported from the designer’s application to class in a managed process that is reliable and fully transparent.
CAD vendors on the case
As software development takes time, right now there is something of a bottleneck in rolling out the OCX format, not on the part of ship designers or class societies, but as 3D software suppliers work to implement it as fast as they can. They are not far off.
As to the future, we are also exploring further digital developments including using AI to compile a database of ships that naval architects can access to study previous designs and sort them based on specific characteristics. This kind of reference set would eventually include 3D models, which would save even more time. Onwards and upwards!
For more information, please contact:
Joonas Määttänen
Project Engineer, Concept Design and Project Services
joonas.maattanen@deltamarin.com
Want to read more? See also our other published blogs.