Mia’s blog series for 2024: The secret ingredient in low-carbon ship design
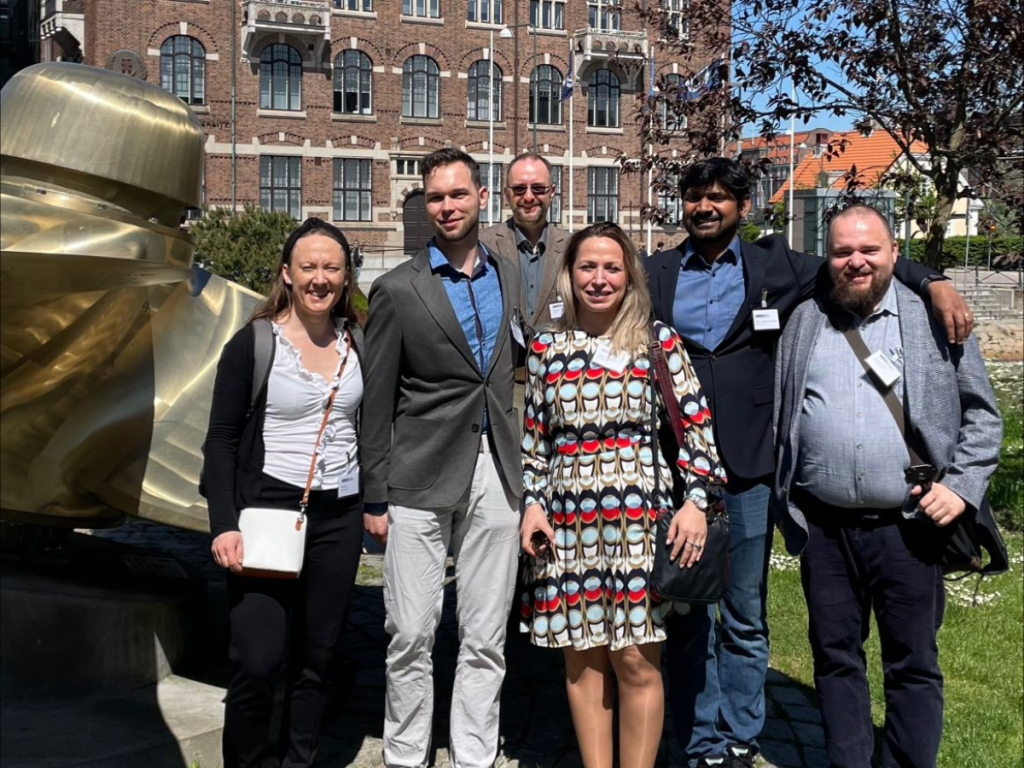
My previous blog was about understanding the big picture and future of heat processes in shipping. This time we move from pure heat systems to ship machinery and energy system analysis with some examples from our newly concluded EU-funded project CHEK.
CHEK will always have a special place in my heart, largely because of the people in our great “CHEK family”. It was also the first EU-project for me personally. I oversaw Deltamarin’s part of the project from planning to execution, so I think that it deserves a moment of reflection in my blog series.
I may have sometimes mentioned in my posts that our sailboat is the primary residence of our family during the summer and we’ve just got back from this year’s adventures. As I happen to have the strongest “sea legs” in our crew, I usually spend a considerable amount of time inside the boat and cook for everyone, no matter what the weather is like. This also inspired me to serve you this blog as it is, fresh from the development oven!
CHEK it out!
Project CHEK was about decarbonising long-distance shipping. Together with 15 consortium partners, we had three years to develop and study two conceptual ship designs: a cruise ship and a bulk carrier. The goal was to reduce greenhouse gas emissions by 99% and achieve at least 50% energy savings, compared to EEDI phase 2 requirements. One of the most visible outcomes of the project to the public was probably the installation of two sails onboard an existing bulk carrier. In addition to this and many other milestones, the CHEK family managed to fulfil the key goals of the project, and the project was listed by the European Commission as a Research and Innovation Project success story. Therefore, even if not every day working on it could be called pure pleasure, I have to say that the project was a success.
Can there be too many cooks in the galley?
I think that the set-up in project CHEK resembled a typical ship design project: we had a wild mixture of various technical alternatives to be considered in the design. In general, it seems like both the scientific community and the industry agree that there is no single best fuel or technology that would be a silver bullet for decarbonisation. Therefore, the new normal for any ship design project today is that we have numerous fundamentally ship-changing alternatives on the table early during the conceptual design that should be analysed.
To be more concrete, on top of the “traditional design task”, each new ship design project is facing a new set of requirements. Three main questions arise at the beginning of a project:
- What is the fuel for the ship that will be considered at the beginning of its operation and which fuels should the ship be ready to bunker in the future?
- Which major energy-saving or emission reduction-related technologies should be included in the ship?
- What is the powertrain and machinery that incorporates the previous two items and brings out the best performance for the entire system?
One of the leading ideas in project CHEK was to explore these three questions as a synthesis, considering a typical operational pattern for the case ships. Without a doubt, multiple variations and complex modelling meant that our “decarbonisation kitchen” started to get very crowded. Our role in project CHEK was, therefore, very central since it included orchestrating the various solutions in the conceptual designs.
The decarbonisation recipe à la CHEK
A longer version of the recipe with insightful pictures can be found, for instance, in the notes from the HIPER conference from 2023 and 2024. A handful of training videos are also available. In addition to these, we have several scientific articles “cooking” regarding the cruise ship and hydrogen fuel. Stay tuned for more information!
A taste of the energy technology synergies
Our bulk carrier concept reached almost 50% digital energy saving compared to a state-of-the-art sailing vessel of similar size. The result was reached as a true symbiosis of technologies and design. The figure below illustrates one of the comparisons of the propulsion and main engine power in two cases. The figures on the left side are related to a “baseline” ship simulation with HFO as fuel, and the figures on the right side illustrate the results of a ship with a combination of new hull and energy saving technologies. The results are illustrated on all global routes that were analysed in the project.
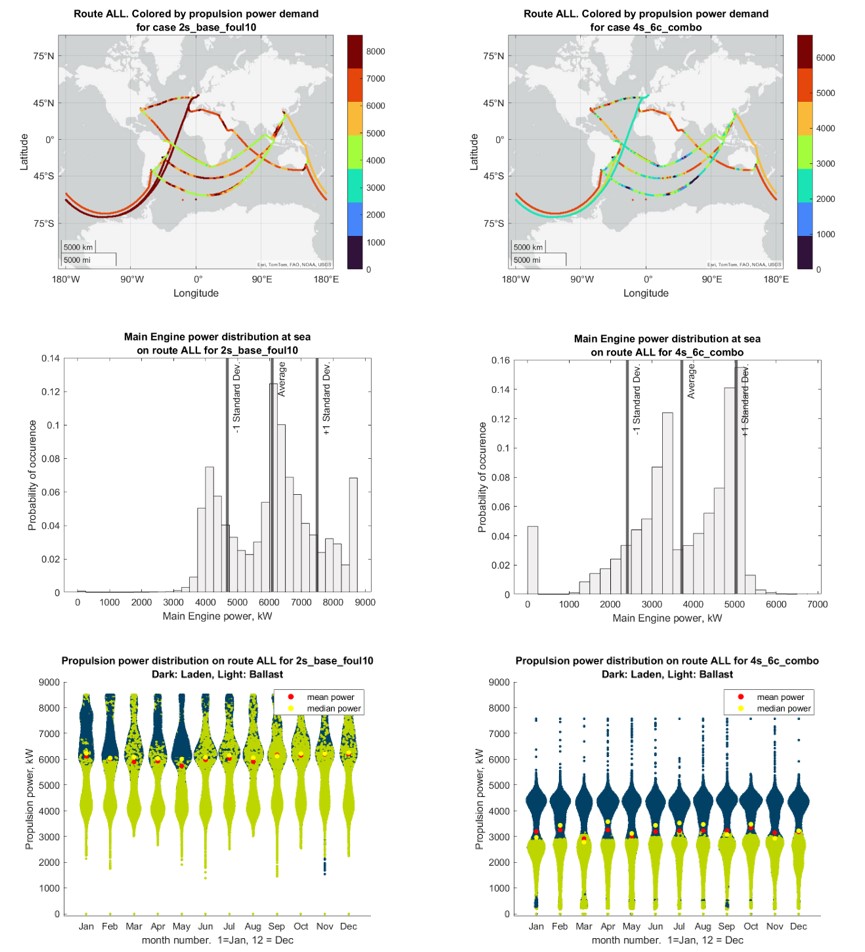
You can see from the figures how the ship propulsion power requirements are reduced from around 6 MW to 3MW with the combination of various drag reduction technologies and wind power. Consequently, various hypothetical engine configurations were studied, including considerably reduced main engine size and a hybrid power train. The machinery parameter optimisation contributed to further energy savings.
When modelling the cruise ship energy system, we made interesting findings especially in hydrogen-fuelled machinery. The cruise ship was analysed on a Mediterranean route, and the first of the results included simulating the ship with HFO as the main fuel. Setting the EEDI-derived energy consumption scaling aside, the results were approximately 21% fuel saving with a combination of various technologies for the cruise ship. When modelling machinery operated with pure hydrogen, but otherwise a similar technology set available for the ship, the results showed 27.5% less fuel energy consumption than a baseline vessel. Several factors in the energy system contributed to these results: improvements in the ship power plant efficiency, but also lower heating requirements for a hydrogen-fuelled ship, leading to lower boiler utilisation and the release of more waste heat for heat-to-electricity conversion.
One generic discovery in CHEK and in many other projects we have carried out is that a ship’s true power requirements on route are often considerably below its installed power. With the CHEK bulker, the reference main engine size was 9.5MW. The results illustrate how increased energy efficiency will push down the power requirements even further, compared to a standard ship. The example simulations did not even consider the impact of weather routing or other voyage optimisation possibilities, which can further contribute to fuel savings.
Let’s have the cake!
In project CHEK, our special focus was on ship energy systems and their modelling. Introducing single equipment or design changes and especially a change of fuel have a holistic impact on a ship’s energy system. When integrating several energy-saving technologies onboard, there is an impact not only on the entire energy system but also between the new pieces of equipment. Since regulations are pushing for reduced emissions from ships, we will eventually have new clean fuels onboard. These fuels are more expensive, or alternatively the ship operator or owner will pay for polluting. Either way, energy-saving is a way to commercially survive and beat the competition.
When I entered this business, energy system modelling was merely seen as the “icing on the cake” rather than a game changer. Nevertheless, now in the middle of various decarbonisation solutions and developing legislation, ship energy system modelling and its related analysis should be seen as a new but important ship design discipline. The simulations can enable correct dimensioning of the equipment, such as ship machinery and fuel storages. In my view, to study design variations on the energy system level as we did in project CHEK is a highly useful screening step in any project. It is done to identify the solutions that we want to proceed with in a more holistic naval architectural analysis and ship design integration on all levels. The energy simulation also enables later comparison of expected performance with the measured data from the ships, providing a platform for design validation.
Finally, we simply cannot afford to skip the analysis of the combined effect of our design choices. Sticking to the traditional way of dimensioning ship fuel storage and propulsion machinery with extensive design margins leads to continuously increasing costs for the ships. I believe that the winners of the future will be those that dare to take the next step in pushing for optimised operation, and dimensioning the machinery to perform best under the most typical conditions.
For more information, please contact
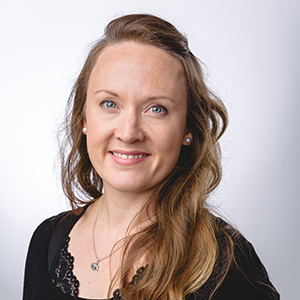